Styreen en nafta met evenredige kwaliteit als virgin materiaal
Plastic2Chemicals Indaver
Naar alle verwachting zal ‘Plastics2Chemicals’ in het vierde kwartaal van dit jaar officieel opstarten. Zowel polystyreen (PS)/geëxtrudeerd polystyreen (XPS) als polyolefinen zullen er worden verwerkt tot secundaire grondstoffen. Mét een dergelijk hoge kwaliteit dat ze zelfs geschikt zijn voor de productie van nieuwe primaire voedselverpakkingen.
Met deze demonstratiefabriek in de Antwerpse haven brengt Indaver een Europese primeur. De doelstellingen van Europa om de hoeveelheid oliegebaseerde kunststofverpakkingen drastisch te verlagen, mogen op zijn minst ambitieus worden genoemd. In die mate zelfs dat velen zich afvragen hoe ooit aan de toekomstige voorwaarden zal kunnen worden voldaan. Voor een grote hoeveelheid plastics bestaan immers nog geen of onvoldoende recyclagemogelijkheden. En wat wel wordt gerecycleerd, is vaak van onvoldoende kwaliteit om als grondstof voor de aanmaak van primaire verpakkingen te worden gebruikt (zeker wat de toepassingen in de voedingsindustrie betreft). Gelukkig zijn er meerdere pioniers die met veel ijver en enthousiasme naar oplossingen voor deze hiaten in de markt zoeken. Een grote naam op dit vlak is de Indaver Groep die bekend staat omwille van haar vele initiatieven op het vlak van duurzaam afvalbeheer. “Al onze projecten zijn goed doordacht en moeten in een reëel businessmodel kaderen,” vertelt Erik Moerman, sales & development director van Plastics2Chemicals. “De focus ligt altijd op het bouwen en opereren van een eigen installatie, maar we zullen niet nalaten om daarrond andere activiteiten te ontwikkelen als de opportuniteit zich stelt. Plastics2Chemicals is op dat vlak een mooi voorbeeld: wat als een idee voor een installatie startte, heeft zich doorheen de jaren ontwikkeld tot een cradle-to-cradle model waarbij Indaver bijna de volledige keten op zich neemt. Services zoals voorbehandeling en logistieke activiteiten versterken de toegevoegde waarde én economische haalbaarheid van de nieuwe plant die toch wel een serieuze investering vereiste. Alleen al de bouw ervan kostte 60 miljoen euro, en dan tellen we daar nog de zeven jaar R&D niet bij. Gelukkig heeft Europa ingezien dat onze innovatie wel eens een revolutie in de recyclagemarkt zou kunnen veroorzaken, met als gevolg dat we 10,5 miljoen euro aan subsidies mochten ontvangen.”
R&D vanuit visie

Het zaadje voor Plastics2Chemicals werd een klein decennium geleden geplant en ontkiemde dankzij de toenemende vraag van de chemische sector naar alternatieven voor fossiele grondstoffen, de wetgeving die alsmaar strenger werd en de groeiende maatschappelijke relevantie die aan recyclage wordt toegekend. “Dat we uiteindelijk voor PS kozen, heeft alles te maken met het feit dat deze afvalstoffen momenteel mechanisch worden verwerkt tot recyclaat dat onvoldoende kwalitatief is om in voedselverpakkingen te worden toegepast,” verduidelijkt Moerman. “Een deel belandt bovendien nog steeds in de verbrandingsoven. Daar tegenover staat dat polystyreen met onze technologie wel perfect tot een hoogwaardig styreen kan worden verwerkt, dat dan weer verder kan worden gepolymeriseerd tot PS dat voor voedselverpakkingen is geschikt. Dus net zoals wanneer fossiel styreen als grondstof wordt aangewend. We wisten dus dat er potentieel én ook wel voldoende aanvoer was. Naast PS hebben we ook een ander polymeertype erbij genomen dat met dezelfde problematiek kampt: polyolefinen (polypropyleen en polyethyleen). Van meet af aan hebben we de focus van onze R&D enerzijds op de doorgedreven verwijdering van de vervuiling gelegd, waarmee we meteen een unieke visie implementeerden. De meeste recyclageoplossingen worden immers niet vanuit het perspectief van het afval ontwikkeld, maar wel vanuit de ontwikkeling van nieuwe technologieën. Anderzijds hebben we hard gewerkt aan het verduurzamen van het recyclageproces. We wisten al snel dat pyrolyse de beste techniek zou zijn, maar deze vraagt veel energie en hangt dus samen met een stevige ecologische voetafdruk. Gelukkig slaagden we erin om die maximaal te reduceren.”
Samen met universiteiten
Het traject startte met bestaande puzzelstukken op zo’n manier te modificeren dat ze samen in een uniek verwerkingsproces op basis van pyrolyse resulteerden. “Dit gebeurde in een eerste fase met een kleine pilootinstallatie die onze ingenieurs samen met de UGent op punt hebben gezet,” vertelt Moerman. “De onderzoekers daar hebben ook gewerkt op de levenscyclusanalyse van de recyclage van kunststoffen. Vervolgens werd de Universiteit Antwerpen in het project betrokken, onder meer voor hun expertise in analyse en nabehandelingstechnieken. Tenslotte is de KULeuven nu bezig met onderzoek om het industriële proces efficiënter te maken door middel van katalysatoren; componenten die we toevoegen aan het pyrolyseproces. Anno 2022 waren we klaar om het labo vaarwel te zeggen en een upgrade naar een echte industriële installatie te maken. Deze is intussen gebouwd en zit momenteel in het stadium van ‘commissioning’”.
Hoogtechnologisch proces
Omwille van het vernieuwende karakter van het proces is ‘Plastics2Chemicals’ in eerste instantie een demonstratiefabriek waar in de komende jaren verder aan de installatie zal worden gesleuteld. In de eerste drie jaar zal de verwerkingscapaciteit ongeveer 26.000 ton per jaar bedragen (met mogelijkheid om die tot 30.000 ton per jaar op te trekken), en dit voor PS en de polyolefinen (processing zal weliswaar in aparte campagnes gebeuren). In 2028 voorziet Indaver de opstart van een tweede lijn. Vanaf dan zullen de twee recyclagelijnen (enerzijds voor PS en anderzijds voor PO) worden gescheiden en zal de gezamenlijke capaciteit 75.000 ton per jaar bedragen. “De huidige lijn is samengesteld met componenten van verschillende leveranciers die deze allemaal op onze toepassing hebben afgestemd”, aldus Moerman. “Zo bestaan er oplossingen voor het distilleren van fossiel styreen, maar niet voor onzuiver styreen dat uit de recyclage van PS-afval komt. Onze pyrolysereactor werd ook aangepast om elektrisch te verwarmen. Op die manier kunnen we de energie van ons grote PV-park en windmolens op de site aanwenden en de ecologische voetafdruk van het proces aanzienlijk reduceren. Als resultaat van al die aangepaste componenten is de som van de gemene delen een compleet nieuw en uniek proces dat nergens anders in Europa - en wellicht ook niet elders in de wereld - haar gelijke kent. Het proces incorporeert veel meer innovatieve technologie dan de gangbare recyclagetechnieken. Daarom is het eindresultaat ook wat duurder dan recyclaat dat bijvoorbeeld via gewone mechanische recyclage wordt bekomen. Maar daar tegenover staan een zuiverheid, kwaliteit en karakteristieken die met ‘virgin’ materiaal vergelijkbaar zijn. In die mate dat onze afnemers met deze secundaire grondstoffen nu markten kunnen aanboren die tot nu toe uit de boot vielen, zoals primaire verpakkingen voor de voedingsindustrie.”
Lokale afzetmarkt
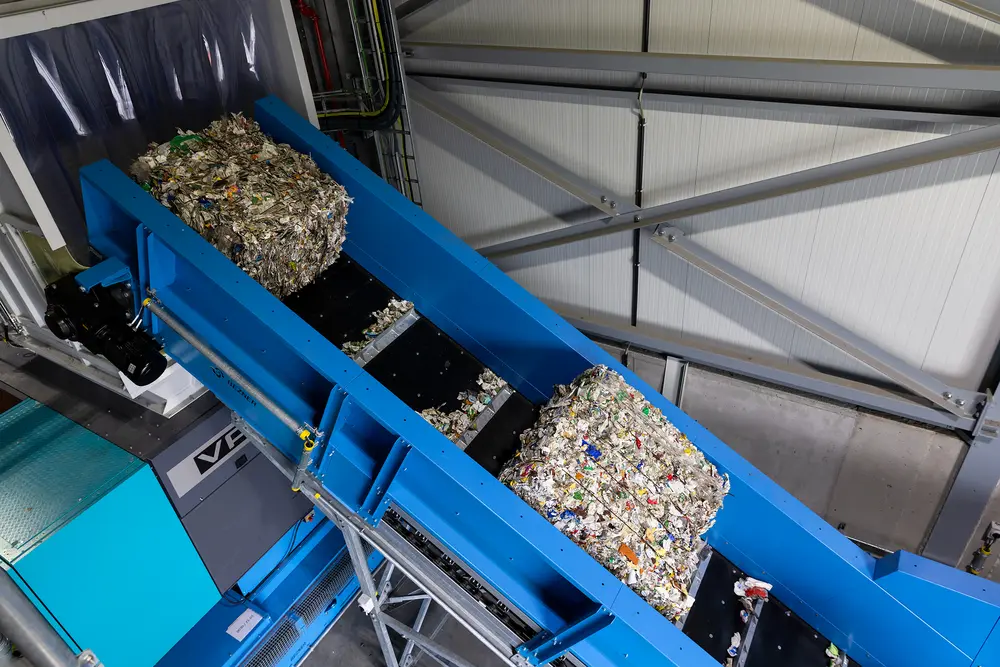
De aanvoer van ‘afval’ zal vanuit meerdere Europese landen gebeuren, gewoonweg omdat de hoeveelheid PS in België kleiner is dan de capaciteit van de fabriek. Polyolefinen zijn er voldoende, maar voor de recyclage ervan heeft FostPlus al contracten met meerdere mechanische verwerkers lopen. “Vandaar dat we onze grondstof gedeeltelijk moeten importeren,” vertelt Moerman. “De ecologische voetafdruk van dit transport wordt gedeeltelijk gecompenseerd door de voornamelijk lokale afzet - in de haven van Antwerpen - van het eindresultaat. Zo zullen Trinseo en Ineos Styrolution de styreen aankopen, terwijl de nafta - dat we van de polyolefinen maken - onder meer naar Total Energies in Antwerpen zal gaan.”
Totale ontzorging
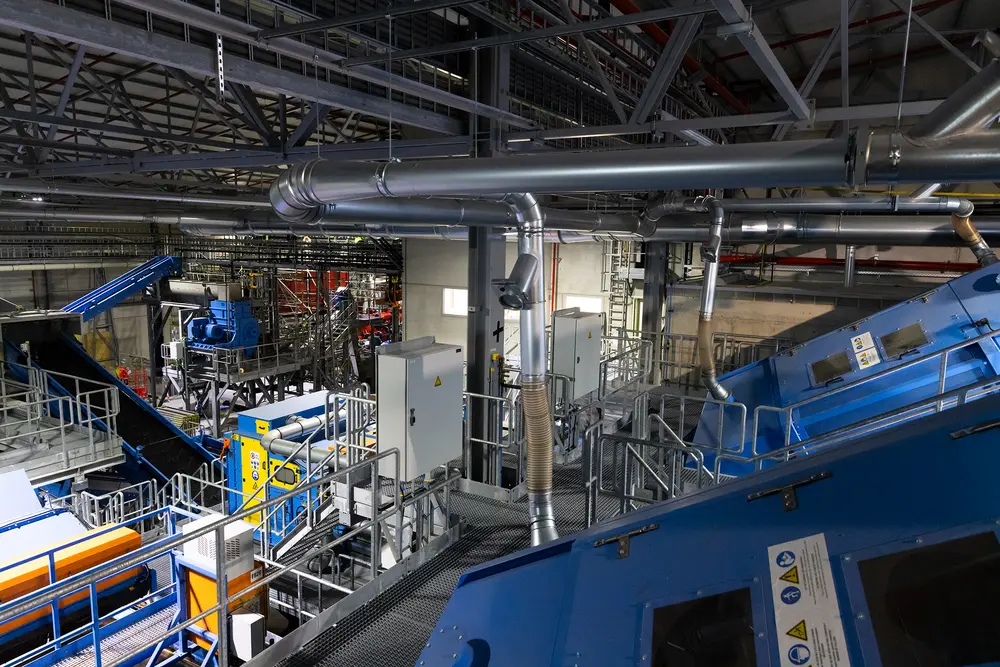
Zoals al eerder aangegeven neemt de Indaver Groep voor styreen alle, en voor de nafta bijna alle stappen na ophaling voor zijn rekening, wat eveneens een uniek gegeven is. In 2020 investeerde ze 35 miljoen euro in de bouw van een sorteerunit in Willebroek. “Wij zorgen er in België mee voordat de polystyreen en de polyolefinen uit het huishoudelijk verpakkingsafval worden gesorteerd en in balen worden geperst,” legt Moerman uit. “Op dezelfde site investeerde Indaver ook 30 miljoen euro in een installatie waarmee we dit afval voorbehandelen en in pellets omzetten. Deze worden vervolgens voor verwerking naar ‘Plastics2Chemicals’ getransporteerd. Dankzij een depolymerisatieproces en de opzuivering met verregaande distillatie van PS ontstaan monomeren die meteen in het productieproces van de klanten inzetbaar zijn. Wij zorgen voor de stockage én een just-in-time levering tot bij de afnemer. De nafta vereist nog een tussenstap met stoomkrakers om tot olifines te komen, iets dat buiten ons expertisedomein valt. Vandaar dat de klanten voor deze secundaire grondstof bedrijven zijn die over dergelijke installaties beschikken. Ook zij worden just-in-time beleverd. Kortom, met dit initiatief profileren we ons een ‘total serviceprovider’ van een bijna gesloten recyclagecirkel, wat het duurzame karakter van dit initiatief nog sterker in de verf zet. Zowel de leverancier van onze grondstof als de afnemers van het recyclaat hoeven niks aan hun processen te veranderen of extra stappen te regelen. Wij zorgen voor een complete ontzorging, waardoor we een extra steentje bijdragen aan het welslagen van de Europese ambities om meer recyclaat en minder ‘virgin’ material in verpakkingen te gebruiken.”
Foto's: Indaver