Du styrène et du naphta de qualité équivalente à la matière vierge
Usine Plastic2Chemicals d’Indaver
Sauf imprévu, 'Plastics2Chemicals' devrait démarrer dans le courant du quatrième trimestre. Tant les PS (polystyrène) et XPS (polystyrène extrudé) que les polyoléfines y seront transformés en matières secondaires, et ce dans une qualité telle qu’ils pourront servir à fabriquer de nouveaux emballages primaires pour aliments.
Avec ce démonstrateur implanté dans le port d’Anvers, Indaver signe une première européenne. Les objectifs de réduction radicale des quantités d’emballages en plastique pétrosourcé que s’est fixés l’Europe peuvent être qualifiés d’ambitieux. Au point même que certains se demandent comment se conformer aux conditions futures. En effet, les possibilités de recyclage restent inexistantes ou insuffisantes pour bon nombre de plastiques. Et la qualité de ce qui est effectivement recyclé ne convient souvent pas à la production d’emballages primaires (en particulier pour des applications dans l’industrie alimentaire). Mais heureusement, des pionniers dynamiques et enthousiastes planchent sur des solutions destinées à combler ces lacunes. Un grand nom dans ce domaine est le groupe Indaver, connu pour ses multiples initiatives au service de la gestion durable des déchets. "Tous nos projets sont mûrement réfléchis et doivent s’inscrire dans un réel modèle économique", souligne Erik Moerman, Sales & Development Director de Plastics2Chemicals. "L’accent est toujours mis sur la construction et l’exploitation de notre propre installation, mais nous ne pouvons pas négliger de développer des activités annexes si l’occasion s’en présente. Plastics2Chemicals en est un bel exemple : ce qui a commencé par une simple idée d’installation a débouché au fil des années sur un modèle cradle-to-cradle, dont Indaver gère pratiquement l’intégralité de la chaîne. Des services tels que le prétraitement et les activités logistiques renforcent à la fois la valeur ajoutée et la faisabilité économique de la nouvelle usine, laquelle a nécessité un sérieux investissement. Rien que sa construction a coûté 60 millions d’euros, sans compter les sept années de R&D. L’Europe a heureusement compris que notre innovation pouvait déclencher une révolution sur le marché du recyclage et nous a octroyé 10,5 millions d’euros de subsides."
Une R&D visionnaire

La graine de Plastics2Chemicals a été semée voici une petite décennie et le projet a éclos à la convergence de trois facteurs: la demande croissante, dans le secteur chimique, d’alternatives aux matières premières fossiles, le durcissement de la législation et la pertinence sociétale accrue attribuée au recyclage. "Si nous avons finalement opté pour le PS, c’est parce que la qualité du recyclat actuellement obtenu par le traitement mécanique de ces déchets d’emballages est insuffisante pour des applications dans des emballages alimentaires", explique Moerman. "En outre, une partie de ce flux finit toujours à l’incinérateur. Notre technologie permet en revanche de transformer le polystyrène en styrène de haute qualité, qui pourra ensuite parfaitement être repolymérisé en PS convenant pour des emballages alimentaires. Donc, exactement comme pour du styrène d’origine fossile. Nous savions que le potentiel était là et que l’approvisionnement serait suffisant. Outre le PS, nous avons aussi pris en charge un autre type de polymère en butte à la même problématique, à savoir les polyoléfines (polypropylène et polyéthylène). Dès le départ, nous avons d’une part axé notre R&D sur l’élimination complète de la contamination, ce pour quoi nous avons immédiatement mis en œuvre une vision unique. La plupart des solutions de recyclage ne sont pas développées sous l’angle du déchet, mais visent la mise au point de nouvelles technologies. D’autre part, nous avons travaillé dur pour rendre le processus de recyclage plus durable. Nous avons su assez vite que la pyrolyse serait la meilleure technique, mais elle consomme beaucoup d’énergie. Nous sommes heureusement parvenus à réduire au maximum son empreinte écologique."
En collaboration avec des universités
Les pièces du puzzle étant identifiées, il a fallu d’abord les modifier pour pouvoir les assembler en un processus de traitement pyrolytique unique. "Ce qui fut fait dans une première phase avec une petite installation pilote mise au point par nos ingénieurs en collaboration avec l’UGent", détaille Moerman. "Les chercheurs y ont également travaillé sur l’analyse de cycle de vie du recyclage des plastiques. L’Université d’Anvers a ensuite été impliquée dans le projet, notamment pour son expertise dans l’analyse et les techniques de post-traitement. Enfin, la KULeuven s’efforce actuellement de rendre le processus industriel plus efficace par l’entremise de catalyseurs : des composants que nous ajoutons au processus de pyrolyse. En 2022, nous étions prêts à abandonner le labo pour passer à une véritable installation industrielle. Celle-ci a entre-temps été construite et se trouve actuellement au stade de la mise en service."
Procédé de haute technologie
Compte tenu du caractère innovant du processus, 'Plastics2Chemicals' est, dans un premier temps, un démonstrateur appelé à recevoir d’autres ajustements au fil des ans. Les trois premières années, la capacité de traitement atteindra environ 26.000 t/an (avec la possibilité de pousser à 30.000 t/an), PS et polyoléfines confondus (qui seront cependant traités par campagnes séparées). Indaver prévoit de démarrer une deuxième ligne en 2028. Après cela, les deux lignes de recyclage (l’une pour le PS et l’autre pour les PO) opéreront séparément, pour une capacité globale de 75.000 t/an. "La ligne actuelle est un assemblage d’équipements de différents fournisseurs, qui les ont tous adaptés à notre application", poursuit Moerman. "Ainsi, des solutions existent pour la distillation du styrène fossile, mais pas pour du styrène impur issu de déchets de PS. Notre réacteur de pyrolyse a aussi été modifié pour être chauffé à l’électricité. De quoi nous permettre de réduire sensiblement l’empreinte écologique du processus en valorisant l’énergie produite par notre vaste parc photovoltaïque et les éoliennes érigées sur le site. Grâce à la modification des différents constituants, la somme des parties compose un processus nouveau et unique qui n’a son pareil nulle part en Europe – et probablement dans le monde. Ce processus incorpore beaucoup plus de technologies innovantes que les techniques de recyclage courantes. Ce qui explique aussi que le résultat final soit un peu plus cher que du recyclat obtenu par la voie mécanique, par exemple. Mais en même temps, la pureté, la qualité et les caractéristiques sont comparables à celles d’un matériau 'vierge'. Au point que nos acheteurs sont désormais en mesure de prospecter des marchés dont ils étaient jusqu’ici exclus avec cette matière secondaire. Comme celui des emballages primaires pour l’industrie alimentaire."
Débouchés locaux
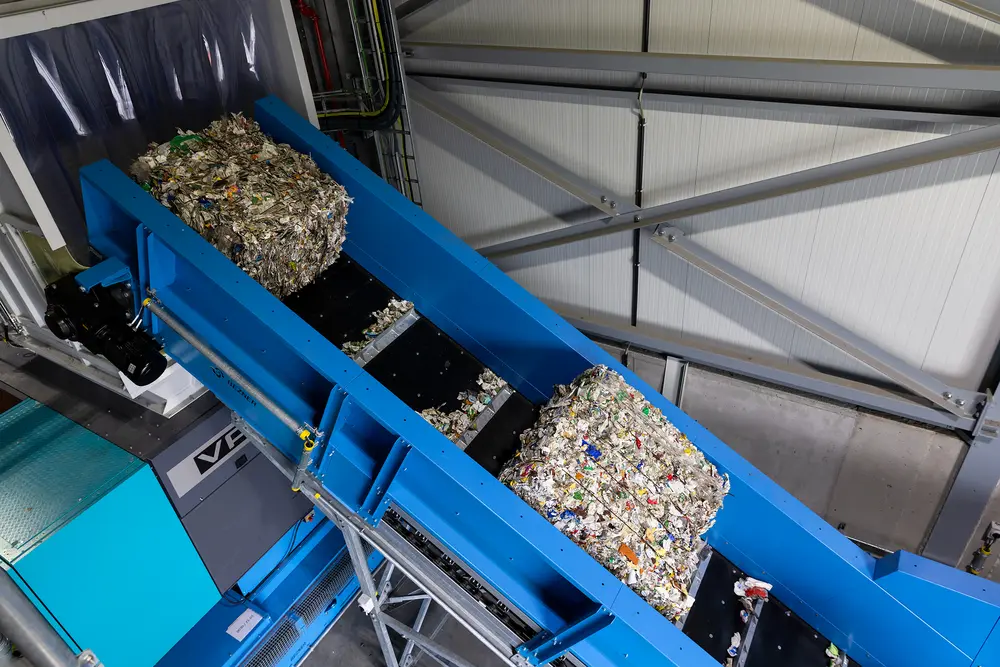
Les 'déchets' seront importés de plusieurs pays européens, pour la bonne et simple raison que la capacité de l’usine est supérieure aux quantités de PS disponibles en Belgique. Les volumes de polyoléfines sont suffisants, mais FostPlus a déjà des contrats avec plusieurs recycleurs mécaniques. "C’est pourquoi nous devons faire venir une partie de notre matière première de l’étranger", dit Moerman. "L’empreinte écologique de ce transport est partiellement compensée par les débouchés essentiellement locaux – dans le port d’Anvers – du résultat final. Trinseo et Ineos Styrolution vont acheter le styrène, tandis que le naphta – que nous extrayons des polyoléfines – partira notamment chez TotalEnergies."
Prise en charge intégrale
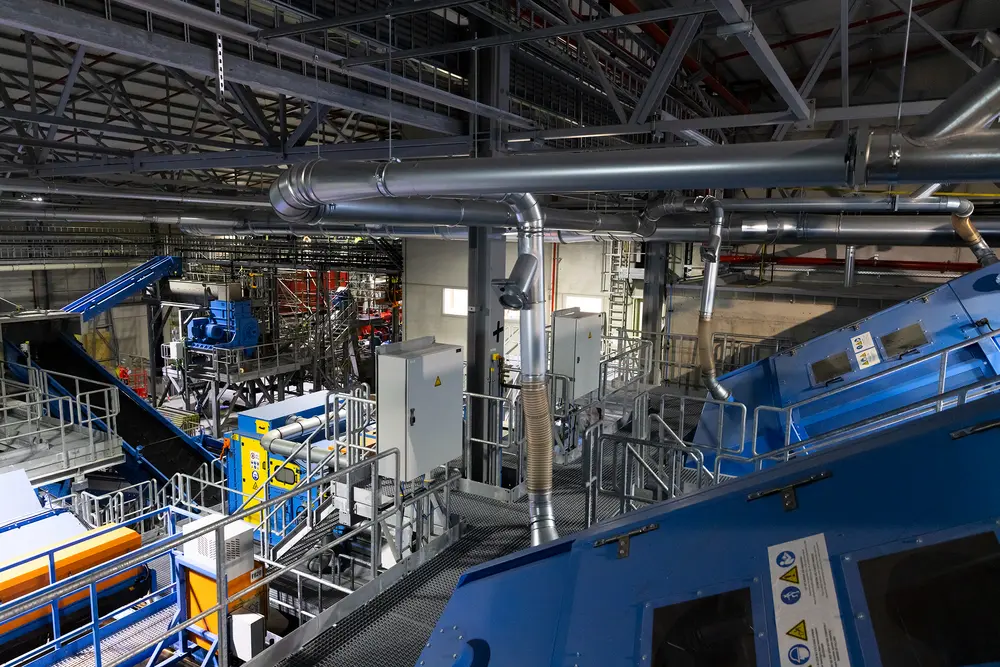
Indaver, on l’a dit, prend en charge l’intégralité des étapes après collecte pour le styrène, et leur quasi-totalité pour le naphta, ce qui est tout aussi unique. En 2020, le groupe a investi 35 millions d’euros dans la construction d’une unité de tri à Willebroek. "Nous contribuons à ce que le polystyrène et les polyoléfines présents dans les déchets d’emballages ménagers en Belgique soient triés et pressés en balles", explique Moerman. "Indaver a aussi investi 30 millions d’euros sur le même site, dans une installation permettant de prétraiter ces déchets et de les transformer en pellets. Ceux-ci sont ensuite transportés à l’usine Plastics2Chemicals. Un processus de dépolymérisation avec épuration par distillation poussée du PS réduit celui-ci en monomères directement utilisables dans le processus de production des clients. Nous assurons le stockage et la livraison à flux tendu jusque chez l’acheteur. Le naphta requiert encore une étape intermédiaire en vapocraqueur pour la production d’oléfines, mais celle-ci sort de notre domaine d’expertise. Cette matière secondaire est donc achetée par des clients équipés des installations ad hoc. Eux aussi sont livrés à flux tendu. Pour résumer, avec cette initiative, nous nous profilons en tant que ‘total service provider’ d’une filière circulaire presque intégralement fermée, ce qui met encore davantage en évidence le caractère durable de cette initiative. Le fournisseur de notre matière première et les acheteurs du recyclat ne doivent rien changer à leurs processus ni y ajouter des étapes. Nous les déchargeons totalement, et apportons ce faisant notre pierre à la réussite des ambitions européennes d’employer plus de recyclat, et moins de matière 'vierge', dans les emballages."
Photographie: Indaver